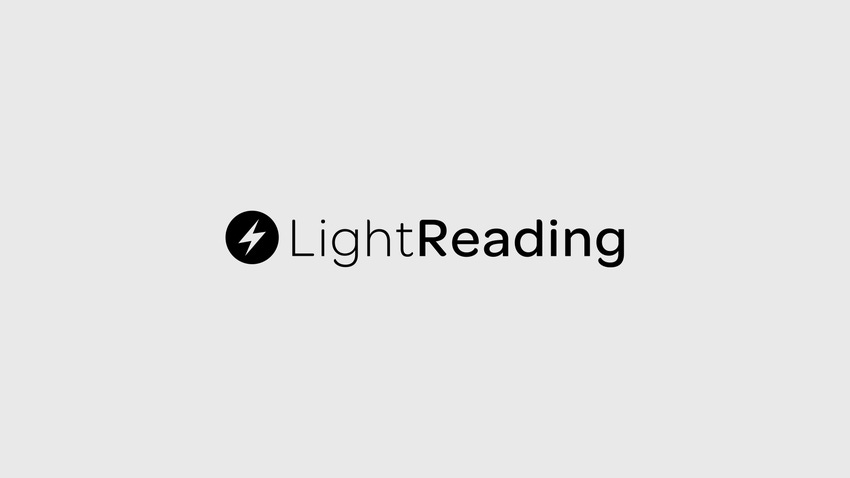
Home to one of Europe's busiest ports, the German city of Hamburg is often snarled up in traffic. Authorities reckon about 10 million containers passed through the docks in 2014. The number is expected to double by the end of 2025. Yet hemmed in by the rest of the city, the port has little room to grow.
Instead, authorities have been making use of emerging technologies to relieve congestion. A "connected logistics" service developed in partnership with Deutsche Telekom AG (NYSE: DT), Germany's biggest telecom player, and SAP AG (NYSE/Frankfurt: SAP), its software giant, employs sensors, wireless connectivity and cloud computing to give port operators an overview of traffic and container movements in and around the facility. It has already led to a reduction in waiting times for parking spaces, claims SAP, and allowed trucking companies to plan their routes more efficiently. "If you can use IT to facilitate faster loading of ships it would actually allow greater exports of German material," says Steve Bell, a senior analyst with Heavy Reading .
Figure 1: Dead Calm The port of Hamburg during one of its quieter moments.
The Hamburg port project illustrates how digital technologies can be used to modernize and benefit a traditional industry. But Germany still features too few examples of such digitalization. Its Mittelstand, a term coined to describe the large sector of small and midsized enterprises (SMEs), is made up heavily of old-school manufacturers that have yet to embrace Internet-era technologies. "Manufacturing is more relevant in Germany than in other industrialized countries, like the UK," says Helmut Figalist, the head of advanced technology for the digital factory division of Siemens AG (NYSE: SI; Frankfurt: SIE), one of Europe's biggest engineering companies. "To stay competitive in this field we need to cope with digitalization challenges."
The overriding fear is that a Germany ill-equipped for the demands of the digital age will fall behind Internet-savvy newcomers in Asia, according to Robin Duke-Woolley, the CEO of analyst firm Beecham Research. That could have dire consequences for Germany's economic prospects. Local hi-tech companies, meanwhile, do not want to see Germany and Europe beaten in the industrial arena as they were in the consumer technology space. "In football terms we feel we gave the first half to the US," says Ingo Marten, the senior vice president of the Internet of Things (IoT) for T-Systems International GmbH , Deutsche Telekom's IT services division.
Germany hopes to safeguard its industrial competitiveness through an initiative it calls Industrie 4.0. The expression draws on the concept of a fourth industrial revolution following previous upheavals that saw the emergence of the steam engine, the development of the assembly line and the arrival of the computer. In the latest revolution, digital and IoT technologies will sweep through the workplace and the factory floor and change them beyond recognition, or so the thinking goes.
While the anglicized term Industry 4.0 is now being used in other parts of the world to describe these forces, Germany's Industrie 4.0 initiative was originally conceived by associations representing specific national interests -- including VDMA (machine builders), ZVEI (electronics) and BITKOM (IT) -- and is now being steered by the German government. Stakeholders including Deutsche Telekom, SAP and Siemens hold regular meetings with government authorities. Working groups have been set up to explore issues such as standardization, research, security and the legal framework. Universities and companies pursuing an Industrie 4.0 agenda can also apply for government funding, says Figalist.
Next page: Spanners in the works
Yet assessing the impact of Industrie 4.0 thus far is not easy. For one thing, it does not appear to have firm targets or objectives against which progress can be measured. Nor is it likely to give rise to specific technologies, or even technical standards. In that respect, it seems focused on aligning Germany with international efforts on standards such as OPC UA (Open Platform Communications Unified Architecture), a protocol for machine-to-machine (M2M) communications.
Organizations involved in Industrie 4.0, including research group Fraunhofer Institute , have also been developing a framework for the initiative. Called RAMI 4.0 (for Reference Architectural Model Industrie 4.0), this attempts to describe the phenomenon in terms of distinct "layers," much like the classic seven-layer Open Systems Interconnect model that is used to break down the various components of a communications network. "RAMI is trying to do something similar for the questions that Industrie 4.0 puts on the table," says Siemens' Figalist. "We need standards on a more detailed level but these will be general technical standards, not Industrie 4.0 standards."
On a less conceptual front, Industrie 4.0 is certainly raising awareness of the importance of digitalization to Germany's competitiveness, according to Nils Herzberg, the senior vice president of IoT at SAP. Case studies are demonstrating how analytics and big data technologies could help factories to realize huge cost savings by shrinking or expanding the size of the workforce based on daily needs. Deutsche Telekom's Marten reckons other "smart factory" technologies are even making some companies think about returning production to Germany from overseas markets like China. "The speed of the digitalization of the Germany economy is increasing," says Herzberg.
Recent research also offers some encouragement. Based on a survey of 235 German industrial companies published last year, PwC Consulting reckons Germany companies will invest about €40 billion ($45 billion) annually in Industrie 4.0 efforts between now and 2020 -- about half of the entire capital expenditure they plan over this period. Productivity is set for an 18% boost thanks to industrial Internet technologies, it adds, while 85% of companies will have rolled out such technologies across all their key business divisions by 2020, up from just 20% last year.
Figure 2: Planned Industrie 4.0 Investments by German Companies Source: PwC.
Industrie 4.0 has "game-changing potential," concurs a separate study from management consultancy Arthur D. Little that came out this month. Companies investing in this area could save between 10% and 50% on operational costs, say the report authors, depending on the particular business function they are addressing.
Spanner in the works
Despite these promises, Industrie 4.0 is not running entirely like a well-oiled machine. Technology proliferation remains a bugbear for any company involved in the industrial Internet. From a connectivity perspective, for example, the recent emergence of low power, wide area (LPWA) network technologies as a rival to cellular has left enterprises with a "bewildering array of credible alternative options," writes Heavy Reading's Bell in a recent article on the Light Reading website. (See How IoT Forked the Mobile Roadmap.)
Germany's broadband strategy is another potential connectivity concern. Deutsche Telekom executives frequently sound warnings that Europe must seize the initiative on 5G or risk lagging other parts of the world in this area, too. Yet Germany could lack the fiber networks that will be needed to support a mixture of bandwidth-hungry mobile services and low-latency IoT applications in future. Deutsche Telekom has no plans to replace most of its last-mile copper connections, preferring to invest in copper-fortifying technologies like vectoring. According to Marten, a national target is to equip nearly all households and businesses with a 50Mbit/s service by the end of 2018. That looks unambitious in comparison with initiatives in some Asian countries. (See Vodafone Calls for Broadband Regulation Shake-Up in Germany.)
As PwC points out, questions also need addressing when it comes to data protection. Indeed, when the companies PwC surveyed were asked where they need most support from policymakers, the creation of a competitive data protection law ranked as the third most popular choice. "If digitalization is really to succeed in manufacturing it will have to solve some major security issues," says Siemens' Figalist.
Figure 3: Top Industrie 4.0 Policy Concerns Among German Companies Source: PwC.
Security concerns in Germany have clearly been exacerbated by revelations in 2013 about US surveillance activities in Europe. Notwithstanding the recent EU-US Privacy Shield pact, which is supposed to guarantee the security of data being sent between Europe and the US, German companies have been worried that data stored with US companies, even on German soil, could fall into US government hands, according to Marten. Regardless of legislative moves, German anxiety about data privacy could stymie the development of certain big data services -- no matter how innocuous they might appear -- such as technologies that gather information about product usage to help manufacturers address faults and make design improvements. (See US Spying Fuels Demand for DT's Cloud Biz.)
Next page: The Catch 22 of Industrie 4.0
In this environment, data security has become integral to the Industrie 4.0 strategy of Deutsche Telekom, which believes it can help Germany's SMEs to overcome their data-protection fears. The operator has been investing in a state-of-the-art data center near Magdeburg, and it frequently touts the attractions of this facility to the security-conscious. On April 1, it plans to launch a new cyber-security business, which will bring together various security departments currently spread across the Group. One of its first products will be a network-encryption service for SMEs. Experton, an analyst firm cited by Deutsche Telekom, reckons the German market for such security offerings will grow by 7% this year.
Figure 6: Digital Vault New data-center facilities based in Germany have become critical to Deutsche Telekom's Industrie 4.0 strategy.
The Catch 22 of Industrie 4.0
Even so, the German telecom incumbent's Industrie 4.0-related activities have not gone as it originally planned. In 2010, as part of a new growth strategy, the operator unveiled a target of generating €1 billion ($1.13 billion) in annual revenues by 2015 from so-called "intelligent network services" aimed largely at the automotive, energy and healthcare sectors. In 2014, however, it managed sales of just €300 million ($338 million) and was forced to concede it would not hit its original revenue goals (it has yet to publish its 2015 results). The overall T-Systems business is also expected to miss a target of generating €7 billion ($7.9 billion) in "external" revenues (that is, from outside the Deutsche Telekom Group) in 2015, having made €5.8 billion ($6.5 billion) in 2014.
Figure 4: Deutsche Telekom's Growth Areas ( euro B) Source: Deutsche Telekom.
Deutsche Telekom has blamed "realignment" at T-Systems -- which has undergone several bouts of restructuring in recent years -- for this setback. A decision to focus on cloud services, and jettison much of the traditional IT business, clearly bears a lot of responsibility for the revenue upset. Yet a broader market malaise could be partly culpable.
In this regard, a bigger problem than the issues of standardization, connectivity and security (although related to them) seems to be the lack of compelling evidence about the business benefits of digitalization. In its 2015 report, PwC flagged the "partly still unclear business cases for the industrial Internet at company level" as a major hurdle. Arthur D. Little says that a "limited number of industrialized examples make it hard to understand the complexity of the topic." Faced with a jumble of technologies and Industrie 4.0 scenarios, C-level executives are having a hard time picking out the ones that could bring them a real competitive advantage, argues the management consultancy.
The availability of detailed case studies, including statistical evidence of cost savings and other operational benefits, could help to get the Industrie 4.0 wheel spinning faster. But some companies that have already profited from investments in digitalization are loth to share their stories. "That's a problem we've always had with M2M -- the best use cases don't get discussed because they are making companies more competitive, and those companies don't want their rivals to catch up," says Duke-Woolley of Beecham Research.
This is the Catch 22 of Industrie 4.0. Businesses are wary of making investments until they better understand the benefits of doing so. Yet they cannot develop that understanding unless early movers overcome a resistance to publicizing their experiences. "Some bigger companies will do it but not talk about it because of competitive advantage," acknowledges Deutsche Telekom's Marten.
Next page: From goods to services
Nevertheless, an early adopter of digital technologies can expect to enjoy a growing advantage over a follower when it comes to profit margins, according to Arthur D. Little. Assuming both had a margin of 10% today, the early adopter's would have grown to 17.4% by 2025, while the follower's would have shrunk slightly to 9.4%.
Figure 5: Margin Development at Companies Investing in Digitalization Source: Arthur D. Little
This finding might address some of the concern about data sharing, although it could prompt further questions about the rationale for Industrie 4.0 investments among late adopters. A spending strategy designed to reduce margin pressure is far less exciting than one aimed at boosting profitability.
From goods to services
Industrie 4.0 might look more attractive to German enterprises if it had more to say about sales growth and service development, rather than efficiency measures. That currently makes it look quite different from the Industrial Internet Consortium (IIC), a non-governmental US initiative founded in March 2014 by AT&T Inc. (NYSE: T), Cisco Systems Inc. (Nasdaq: CSCO), General Electric Co. (NYSE: GE) (GE), IBM Corp. (NYSE: IBM) and Intel Corp. (Nasdaq: INTC). "Industrie 4.0 in its pure sense is about improving internal processes and product offerings, while IIC is also about moving companies from being product-only players to product-and-service ones," says Duke-Woolley. (See US Giants Carve Out Role in the Industrial IoT .)
Perhaps no organization encapsulates this better than GE. Having already made a shift into the services area, the conglomerate continues to look at ways of selling traditional products on a pay-for-use basis, rather than as standalone capital assets. This mirrors developments that have already taken place in the enterprise software and digital music markets, where on-premises systems and CD ownership are becoming increasingly anachronistic. "GE has a $200 billion order book for services relating to products and if they can improve that by just 1% they will boost the bottom line by $2 billion," says Duke-Woolley. "It's worth spending $1 billion a year to try to achieve that because it's going to be a continuous improvement."
Want to know more about the Internet of Things? Check out our dedicated IoT content channel here on Light Reading.
Service development is likely to rise up the Industrie 4.0 agenda as its objectives become increasingly "conflated" with those of the IIC, according to Duke-Woolley. PwC reckons the digitalization of services promises additional revenues of between 2% and 3% a year on average, or an extra €30 billion ($34 billion) annually across the whole of Germany.
Companies like Kaeser Kompressoren are already demonstrating the possibilities. Traditionally a manufacturer of air compressors, Kaeser is exploring a business model of selling cubic meters of compressed air rather than actual compressors. "We've already seen this approach with office printers and other industries will go that way," says SAP's Herzberg. "Nobody wants to be a proud owner of ten compressors or 100 forklifts -- they just want to use them." If other Mittelstand players do make the same jump from manufacturing to selling services, Industrie 4.0 will have been revolutionary indeed.
— Iain Morris,
, News Editor, Light Reading
Read more about:
EuropeAbout the Author(s)
You May Also Like